Could a HUD-funded 3D-printing project transform housing in Alaska?
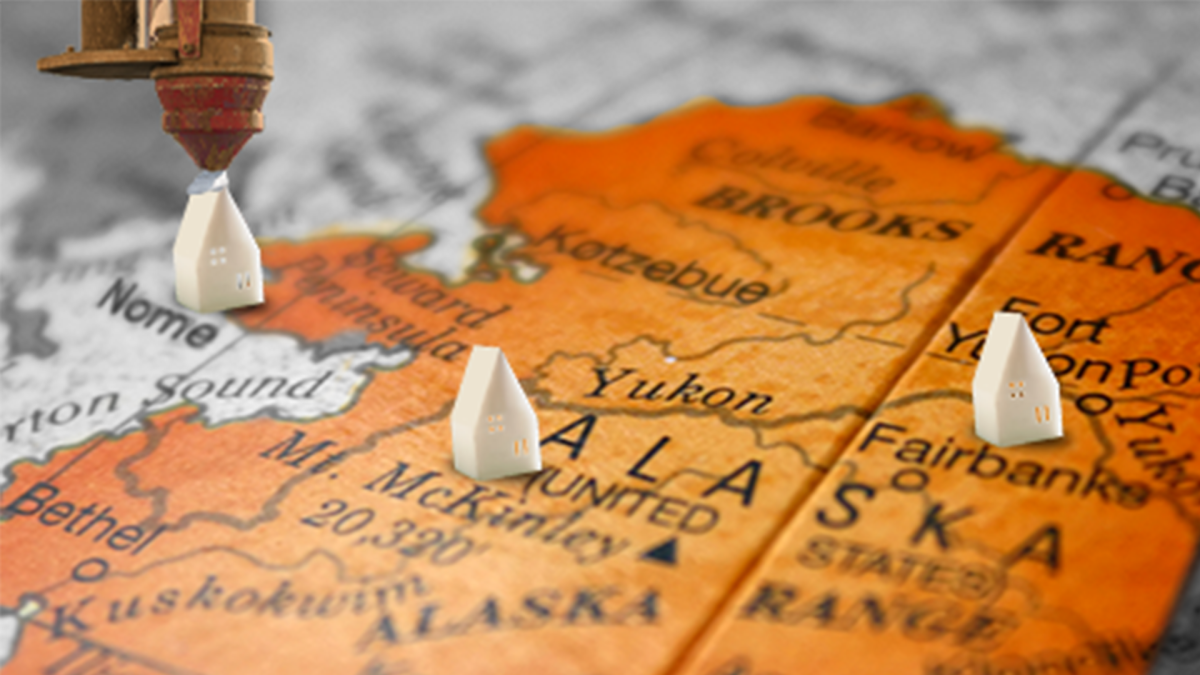
To build a home in Nome, Alaska, is to take an encyclopedia’s worth of knowledge about ideal construction conditions and heave that text directly into the Bering Sea.
From erecting wooden structures on subarctic tundra to eating the exorbitant costs required to ship materials to the wind-whipped coastal city that’s inaccessible by road, the challenges in homebuilding there are innumerable. And that doesn’t even account for an igloo-sized elephant in the room.
“When it gets 30 below and a 20 mile-an-hour wind, that’s pretty cold for everyone up here,” said Glenn Steckman, Nome’s recently departed city manager.
Next summer, many of those homebuilding impediments could begin to crumble thanks to a Department of Housing and Urban Development-funded project that will use 3D-printing technology to construct an affordable housing unit in Nome, the culmination of a yearslong effort from federal, state and local governments, private industry and academia.
The $600,000 HUD issued to Nome is part of a $1.6 million matching grant program to fund the development and testing of a mobile 3D printer built specifically for use in the unforgiving Alaskan clime. After months of testing in Fairbanks and suburban Anchorage, the 3D printer will be transported to the remote town on the southern Seward Peninsula known best for its turn-of-the-century gold rush, where the machine will build a home that stakeholders hope can serve as a proof of concept for rural Alaska and beyond.
“There’s obviously very pressing local needs in Nome,” said Tanaya Srini, senior advisor for innovation, policy development and research at HUD. “But I think we’re also thinking about how it can inform the broader needs across markets.”
In Alaska, where the cost of living is well above the national average and the housing stock is increasingly outdated, 3D printing advocates see a perfect opportunity to put their technology to the test. The researchers who made the case for Nome’s viability have waited more than three long years for that day to come.
An ‘ideal location’ for 3D-printed homes
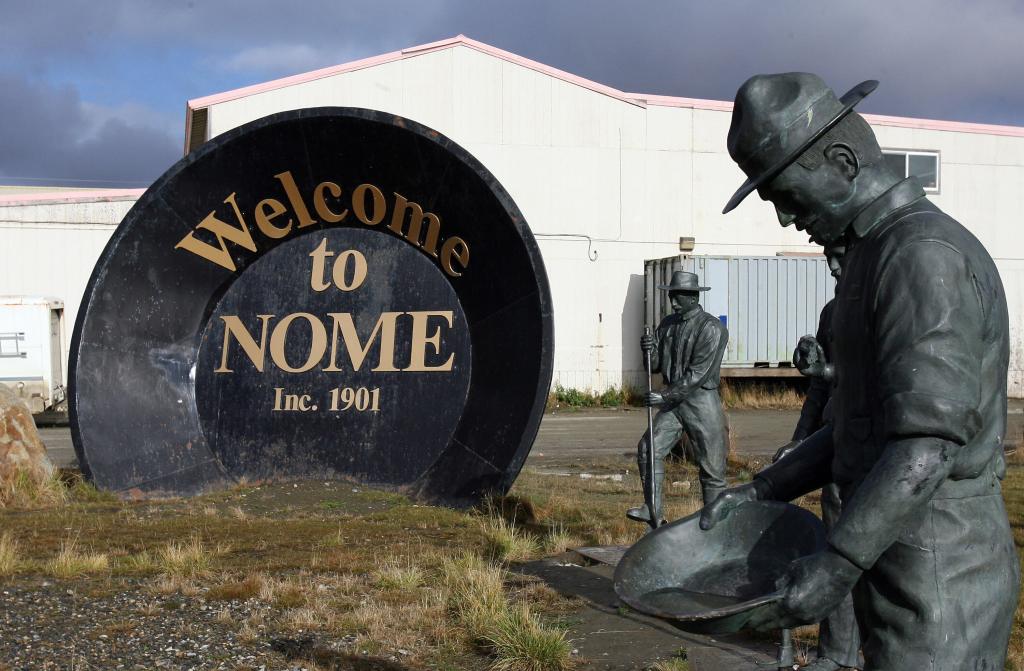
Overcrowded and inefficient, with a slow rate of construction that doesn’t meet demand. That’s what the Alaska Housing Finance Corporation found in its 2018 housing assessment for the state’s rural areas. Almost 79,000 households were spending more than 30% of their income on housing-related costs, the report noted, exceeding a threshold that, according to HUD, impacts the ability to pay for other basic needs.
It was under the shadow of that report that the AHFC commissioned the nonprofit Xtreme Habitats Institute to conduct a feasibility study on 3D-printed homes in rural Alaska. The findings, released in 2021, detailed challenges ranging from inapplicable building codes to logistical nightmares in transporting equipment and materials to far-flung regions.
But while those challenges merited “heavy scrutiny,” the report’s authors arrived at the conclusion that the technology possessed the “ability to construct high-quality, affordable houses and communities, at a much faster pace, throughout rural Alaska including the Alaskan Arctic.” There was a “high likelihood” that 3D printing “could be a viable, cost-effective alternative to conventional wood frame construction,” the authors added.
Jimmy Ord, AHFC’s director of research & rural development, said in an email that Nome was quickly identified as a potentially “ideal location” to test-build a 3D-printed home.
“It is a community that needs housing, has local material for printing, and is semi-rural so an opportunity exists to work through workforce, shipping, and other logistics,” Ord said. “If the logistics of using a 3D printer to build a house with local materials can be worked out … in a semi-rural community, it might open opportunities for constructing housing elsewhere in the state.”
That feasibility study turned out to be one of the primary drivers behind HUD’s decision to fund the project, according to Srini, who pointed specifically to the reduction in build time and the cost savings that come with it.
External framing of a house using conventional construction methods can take two to three months in rural Alaska, the report said, with potential delays due to weather and the limited availability of labor. With 3D printing — which will source piles of limestone, sand, gravel and other local materials for a concrete mixture to be printed in layers — that timeline is slashed to one to three days.
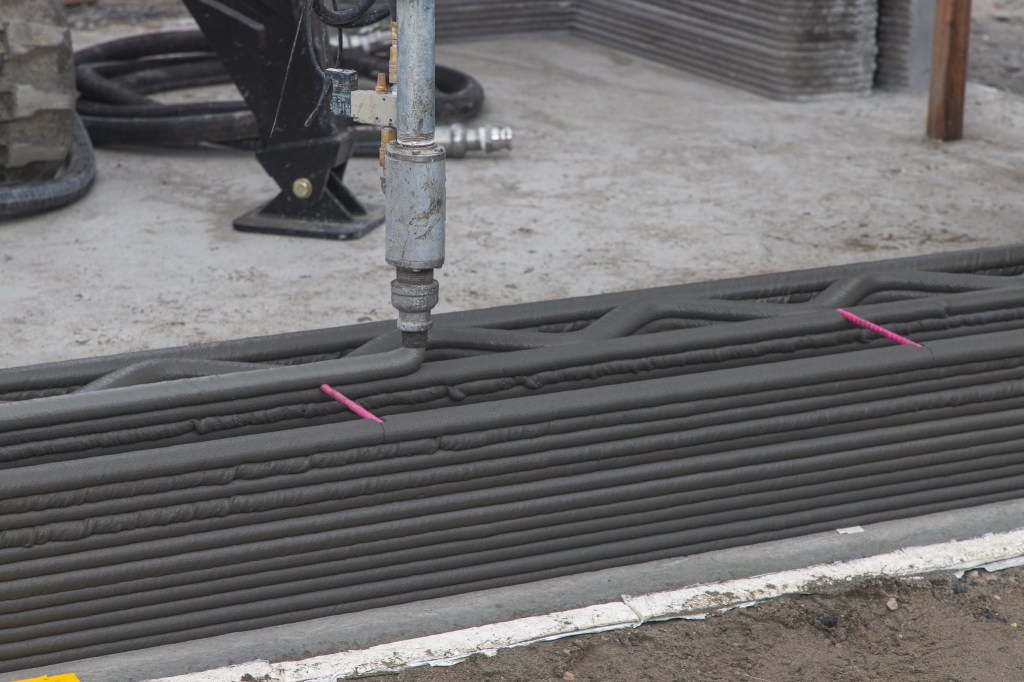
In Nome, where traditional construction costs run roughly 70% higher than in Fairbanks, the savings from that dramatically pared-down schedule would be significant.
“To buy a $600,000, 1,200-square-foot house, you have to have a substantial income, and a lot of our residents don’t have that income,” Steckman said. “So if we can get the housing costs down between $360,000-$400,000 … that is going to allow more people to move from a landlord relationship to a homeowner relationship.”
Alaska isn’t a one-size-fits-all kind of place, Ord cautioned — just because 3D printing may make sense for Nome doesn’t mean that it will work elsewhere in a state known for its diversity of resources, geography, climate, infrastructure and governance. But the AHFC is hopeful that the project “yields positive outcomes that drive further economic impact down the road,” Ord said.
Much of that hope lies in what a team of engineers and designers was able to produce more than 4,000 miles and four time zones away.
Designing a community on tundra
José Pinto Duarte can’t exactly pinpoint the year in which his fascination with 3D printing began, but the memory of his first big idea is crystal clear. It was the mid-1990s when Duarte, then a PhD student in architecture at MIT focused on design and computation, started work on what he termed the “automated generation and fabrication of designs.”
After writing a thesis on that topic and immersing himself more in the technology, Duarte zeroed in on the mass customization of housing, eventually leading him in 2016 to Penn State, where he directs the university’s Stuckeman Center for Design Computing and helped establish its Additive Construction Lab.
In State College, Duarte found his people: designers, engineers, architects, researchers and entrepreneurs, all bonded by the goal of using 3D-printing technology to build housing. In 2021, Duarte and four colleagues founded X-Hab 3D, a move that came after Alaska’s head of economic development asked company CEO Bruce Kraselsky to help identify new technologies to address the state’s rural housing challenges.
While Duarte said the company’s overarching goal is to create 3D concrete printing solutions for the construction industry and “transfer the technology from the lab to the market,” the Alaska project was immediately top of mind. And it began with a surprisingly logical pivot.
Duarte and his X-Hab 3D and AddConLab colleagues had been working on a NASA competition to design houses that could be built on Mars. Myriad differences between the Red Planet and the Last Frontier aside, there were some common threads for the team to pull.
“It’s easier than Mars, obviously, but it’s very similar in the sense it’s an isolated place,” Duarte said. “Alaska is a very difficult environment because of the cold temperature, strong winds. … Our idea was, well, if we succeed in doing this in Alaska, it could work anywhere.”
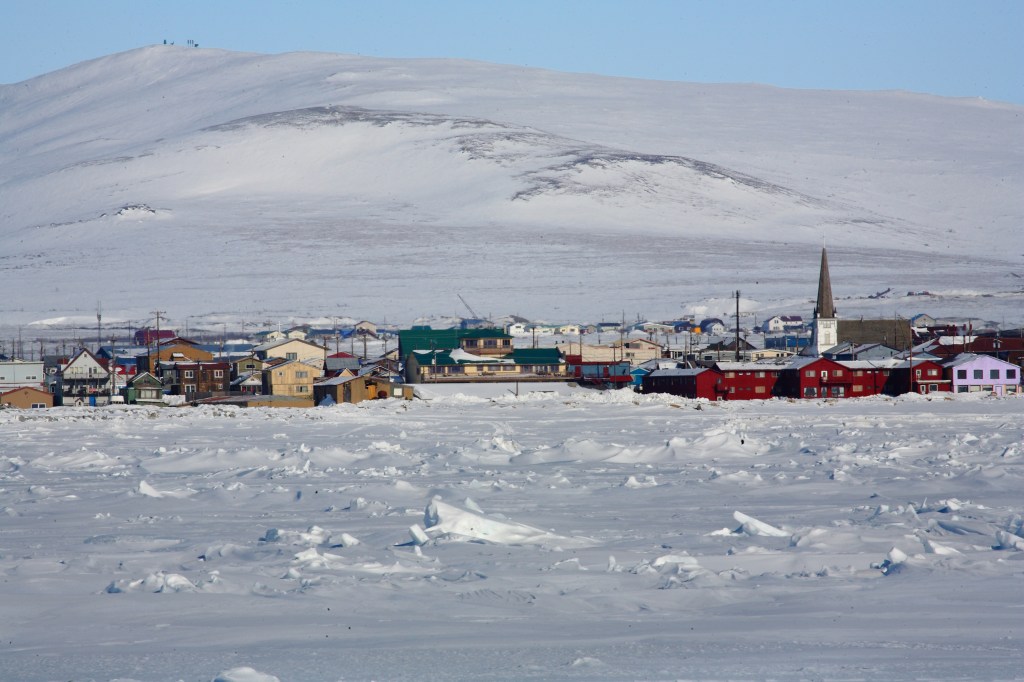
Beyond the obvious climate-related hurdles of building during Nome’s extremely abbreviated summer construction season, there’s “an interesting soil challenge” that also must be taken into account, according to Steckman.
“We have tundra, and building on tundra is possible,” Steckman said — but it’s complicated. “Then we also have what we call disturbed land, land that has been turned over for whatever reason, or is more rocky and doesn’t have … an ice shelf.”
Srini said the inconsistency of Nome’s land makes the mobility and “expeditionary” capabilities of the 3D printer especially critical. Those features mean that the printer “can move itself; it’s basically on tracks,” she said. “Its mobility is really important in terms of what a difficult-to-reach area Nome is.”
Mobility is also crucial because of the sheer size of the machine, which weighs over 12,000 pounds. Keith Comstock, executive director of the Xtreme Habitats Institute, said the unit needed to be able to be “backed off a truck or a barge or a plane” and then transported to a site with potentially inconsistent terrain, as opposed to using a stationary gantry printing system.
“What we have now is a system that maybe takes three people to operate successfully,” he said. “Our goal would be to have one that takes zero people to operate effectively.”
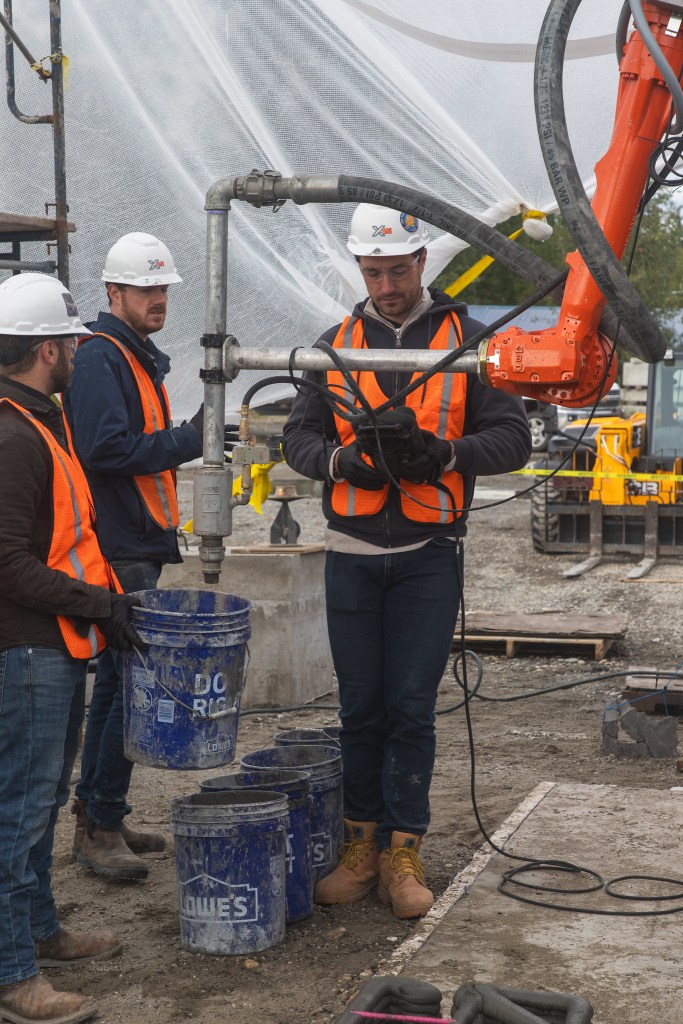
All of those considerations were part of Duarte’s calculus as he and his colleagues moved forward on what he called a truly “collaborative effort.” Duarte’s main areas of focus were developing the software and algorithms that power the printer, and designing the architecture of the housing unit that will be built in Nome.
Software and design decisions were informed by a trip to Alaska last year that gave the team a chance to scout the area for building sites and meet with Nome officials and representatives of the area’s indigenous community, the target population for future affordable housing units. What resulted from that visit was the identification of a build site where the soil is relatively stable and a design concept that would be replicable and customizable.
“We are not just designing a house — it’s a system to design houses,” Duarte said, drawing on his decades of work on mass customization. “So you basically design a system that’s based on a set of rules, and you can use the rules to design customized houses.”
Nearly three years after X-Hab 3D was founded to take on Alaska’s housing challenge, the printer was ready for its long trip into the far northwest.
Training days begin
Standing 8 feet tall with an 11-foot wingspan when its outriggers are fully deployed, the 3D printer was loaded into a truck earlier this summer for a 4,000-mile-plus journey. Making its way from Pennsylvania through the U.S. and Canada, the printer finally arrived at one of its pre-Nome way stations in Fairbanks, where it was treated to a hero’s welcome in late July.
The printer, known as Betsy, was put through the paces near the home of Alaska’s flagship university, with representatives from the city of Nome, HUD, Penn State, AFHC, X-Hab 3D, Xtreme Habitats, the National Renewable Energy Lab, the Denali Commission and others on hand for a 3D-printing test and demonstration.
“I can’t emphasize enough how mind-blowing it was being in Alaska,” Srini said. “As a housing researcher that understands the housing crisis we’re in, it is so acute in Alaska, and you really can only start to understand it when you are in the Arctic tundra.”
The printer’s performance in those frigid temperatures will be assessed over the course of the next several months. While the finished product in Nome will be a three-bedroom, 1,200-square-foot house, the testing happening now is focused on the printing of smaller buildings, with sensors and monitors placed in those structures to give researchers a sense of how the units handle the cold.
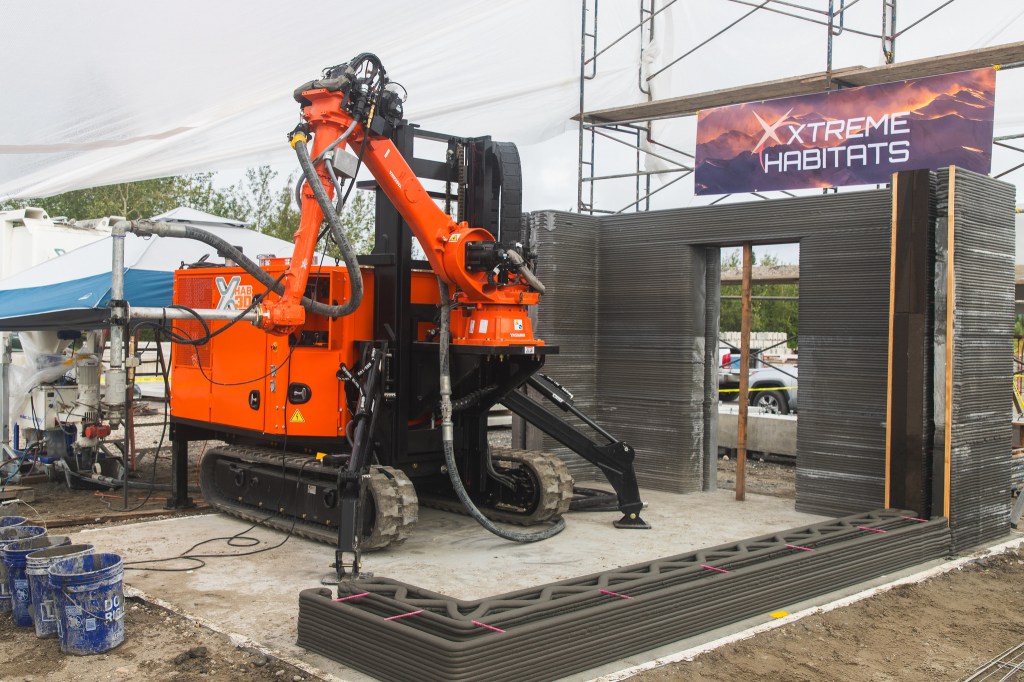
With the printer now stationed 40 miles away from Anchorage in Palmer, the local 528 cement masons and plasterers labor union has been enlisted by Xtreme Habitats in these tests, providing training for people “who work with concrete for a living, whether it’s building foundations or walls,” Comstock said. “We have a tool — a very advanced tool — but in order to go to the next step, it has to be in the hands of artisans.”
When the printer reaches its final destination in July, arriving in Nome either by barge or military aircraft, it will be greeted by a city teeming with anticipation — and leaders keenly aware of the considerable stakes. Nome’s present-day problem of not having enough affordable housing to accommodate its 3,700 or so residents is sure to worsen thanks to an influx of newcomers expected in the coming years.
Construction has already begun on a multimillion-dollar expansion of the port of Nome that will make it the country’s first deepwater port in the Arctic. That project will increase the need for housing in Nome, as will the general recognition of the city’s growing geo-strategic importance. Department of Defense officials have made recent trips to Nome — just a one-hour flight from Chukotka, Russia — as part of a new Arctic strategy.
As Nome prepares for the inevitable changes that come with development of that kind, excitement for that first 3D-printed house is growing among residents, according to Steckman, who Srini called “an enormous champion” of the project and key to making HUD believe in the city as the right place to build.
Before leaving Nome in August to take over as city manager in Cambridge, Md., Steckman said he “received a lot of positive comments” about the project — mixed with a healthy dose of skepticism from people attuned to the area’s building challenges.
But if the initial build is successful, a fundamental change in how construction takes place in disadvantaged areas could be ushered in, with the vision for a 3D-printed and customized affordable housing community in Nome finally realized.
“There is such a need for quality housing, and I do believe that this project, this type of construction, could fulfill that need,” Steckman said. Residents have been asking, “will it work in Nome? And I believe it will.”